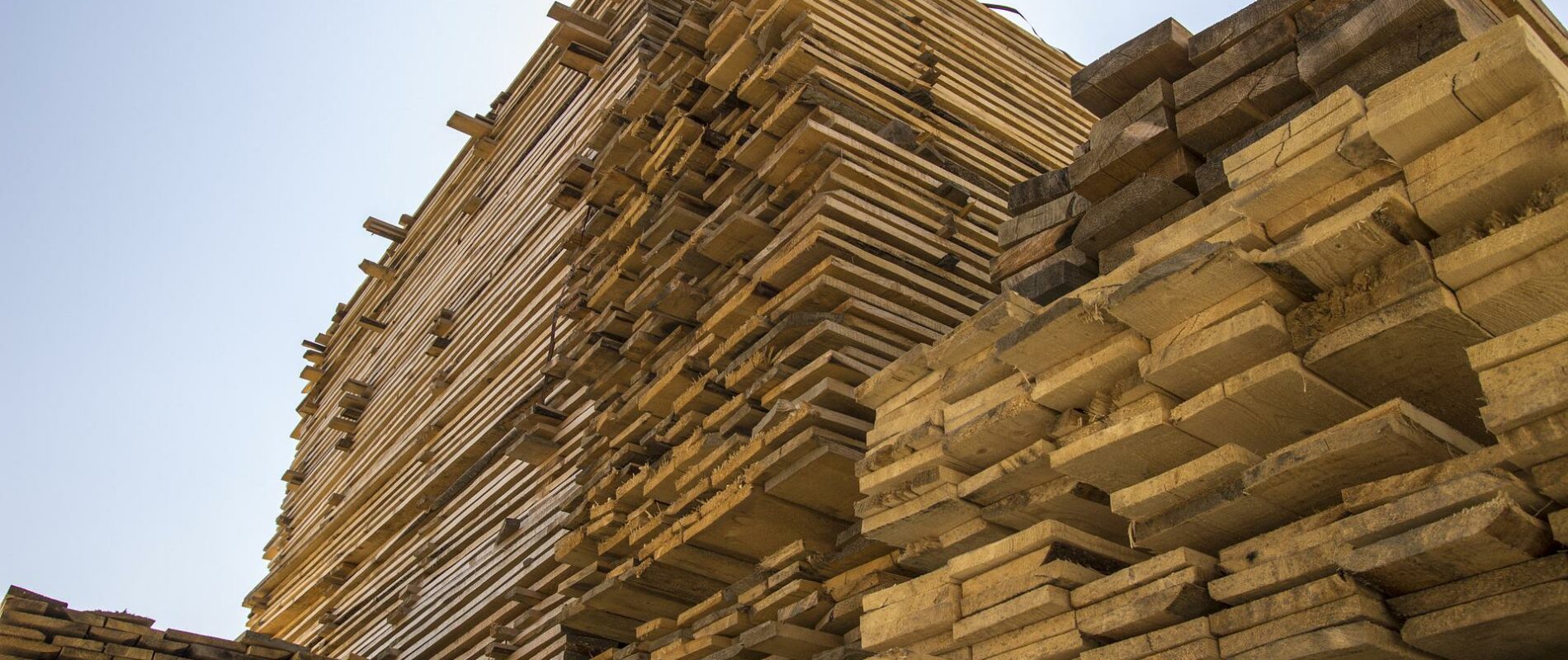
Our Process
Do you have any other questions? Do not hesitate to contact us!
Whether you are unclear about something, want a no-obligation quotation or require a specific solution, we are here for you.
Get in touch
Phone: +507 6964 9631
Mail: info@xopatimber.com
At XOPA Timber, we pride ourselves on our transparent and responsible sourcing practices in Nicaragua. To provide our clients with a thorough understanding of our process, we have outlined each step of the journey, from tree harvesting to the final export of our high-quality timber products.
1. Felling
The first step in the process is to carefully and selectively fell trees in the certified plantations we source from. This ensures minimal impact on the environment while allowing for sustainable forest management. Our partners follow strict guidelines to ensure that only the trees suitable for harvest are chosen, leaving the rest of the forest to continue thriving.
2. Extraction to the Yard
Once the trees are felled, they are transported from the forest to the lumberyard. This process is carried out with utmost care to avoid damaging the logs and to maintain their high quality. The transportation method is chosen based on factors such as terrain, distance, and log size, with a focus on minimizing environmental impact.
3. Log Classification
In the lumberyard, the logs are sorted and classified based on their size, quality, and species. This ensures that we can meet the specific needs of our clients and maintain a high level of product consistency. Proper log classification also allows for more efficient sawing and processing, resulting in less waste.
4. Sawing
The logs are then sawn into rough lumber in accordance with the desired dimensions and specifications. Our partners utilize modern sawing equipment to ensure the accuracy and efficiency of this process. The sawing technique is selected based on the type of wood and the intended use of the final product.
5. Pre-Drying
Following the sawing process, the rough lumber undergoes a pre-drying stage to remove excess moisture. This stage is crucial for preventing warping and other defects that can occur during the drying process. The pre-drying process typically involves air-drying the lumber outdoors or in covered spaces, allowing for natural moisture evaporation.
6. Kiln Drying
Next, the pre-dried lumber is placed in a kiln to achieve the ideal moisture content. Kiln drying ensures the stability and durability of the wood, preparing it for further processing and eventual use in various applications. The kiln-drying process is carefully monitored and controlled to prevent over-drying or uneven moisture content in the lumber.
7. Dried Lumber Classification
After the kiln-drying process, the dried lumber is sorted and classified once again, based on its quality and final moisture content. This step ensures that we only supply our clients with high-quality timber products. Proper classification of the dried lumber also helps in identifying any potential defects that may have occurred during the drying process.
8. Molding
The dried lumber is then processed through molding machines to create the final timber products, such as planks, beams, or moldings. Our partners ensure that each product meets high standards of quality and precision. Molding may also involve other processes such as planing, sanding, or finishing, depending on the specific requirements of the final product.
9. Exporting
Finally, the finished timber products are prepared for export to our clients in Europe. We handle all logistics and documentation required for international shipping, ensuring a seamless and hassle-free experience for our customers. Our commitment to efficient logistics management allows us to deliver the timber products promptly and at competitive prices.
XOPA Timber
Versatec Tower
Calle 50
Panama City
Panama
email: info@xopatimber.com
tel: +507 6964 9631